EPS teams up with GIT for propeller coatings
The extensive application will maximize vessel performance with GIT’s eco-friendly, highly durable, and ultra-low friction foul release coating.
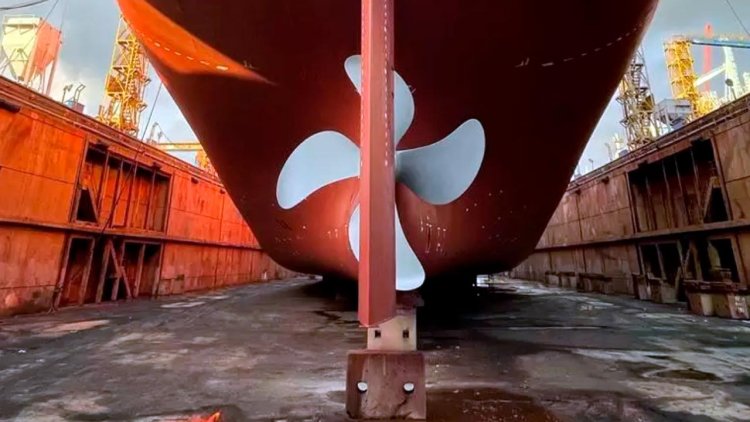
Eastern Pacific Shipping (EPS) continues to drive decarbonization by implementing Graphite Innovation & Technologies (GIT) graphene-based, biocide-free propeller coating across its fleet.
This propeller coating – XGIT-PROP – is an extremely effective way to improve and maintain CII rating over the drydocking cycle.
The two companies started working together a year ago. EPS applied XGIT-PROP on the propeller of an LPG tanker, QUEBEC. Since application, the vessel has seen improved vessel performance, and has maintained its CII rating. Because of that, EPS decided to expand the adoption of the technology and plans to apply the coating on 15 vessels drydocking in 2023 and 2024.
XGIT-PROP is a graphene-based eco-friendly propeller coating that improves propulsion efficiency while keeping propeller surface smooth and free from biofouling. Applying this coating ensures no harmful toxins and biocides are released into the ocean. This adoption supports EPS’s ambitions in reducing GHG emissions and helps the company achieve aggressive sustainability goals.
Pavlos Karagiannidis, Fleet Optimisation Manager at EPS, stated:
“We see GIT’s propeller coatings as part of our portfolio of solutions to achieve long-term fuel efficiency and reduce emissions. We are pushing to make a positive impact on our oceans, and see GIT and their coatings as a key way to do that. This is another sustainable step forward for our company.”
As a sustainable coatings company, GIT has developed several marine coatings for fleets that are interested in reducing their impact on the environment while improving vessel performance. GIT’s XGIT-PROP is a 3-layer graphene-based coating technology that is specifically designed to withstand harsh operational conditions. It had a powerful ability to release biofouling while maintaining smooth surface and reducing the need for propeller ‘polishings’. It also maintains the propulsive efficiency of the propeller and reduces damage due to cavitation, thereby lowering noise emissions.